Project Name
PROJECT
Quality Water Management Brings Struggling Water District Into Compliance
Quality Water Management approached a water district that was under an enforcement order and being fined for non-compliance with Colorado clean water regulations. Within 9 months of working with Quality Water Management, the district was back in compliance and set up for success.
The district was under an enforcement order and being fined for non-compliance with Colorado clean water regulations. Here are the violations that the district was experiencing when the board decided to consult with QWM:
-
Supplier’s groundwater well did not provide adequate protection of source water
-
The Treatment Facility chlorine pump was non operational due a faulty socket
-
Excessive pooling of water via large leak in the pump house
-
Excessive rusting of metal surfaces due to the pooling of water
-
Black mold present on substantial portions of the ceiling including above and next to the finished water storage access hatch
-
Failure to have a monitoring plan
-
Failure to monitor for lead and copper
-
Failure to have a Backflow Prevention and Cross-Connection Control Program
The water district had a sizable hurdle to overcome by the time Quality Water Management became involved. Quality Water Management began to line up the requisite professionals and develop plans to address each of the violations. This is how Quality Water Management resolved each of the violations:
Violation: Supplier’s groundwater well did not provide adequate protection of source water
Resolution:
-
Replaced the well pump
-
Adjusted the wellhead cap
-
Rewired the electrical disconnect box
-
Sealed all points of possible intrusion
Violation: The Treatment Facility chlorine pump was non operational due a faulty socket
Resolution:
-
Repaired the electrical outlet
-
Modified the SCADA system to operate the chlorine pump whenever the well pumps are activated
Violation: Excessive pooling of water via large leak in the pump house
Resolution:
-
Assessed leaks in pressure pumps and Cla-Val valves
-
Repaired, rebuilt, and replaced equipment that had failed seals or had reached the end of expected life of service
-
Modified setpoints to optimize system target pressure and prevent short-cycling of pumps which caused premature failures
-
Installed new Variable Frequency Drives and modified SCADA programming to maintain the most effective running performance of pumps
Violation: Excessive rusting of metal surfaces due to the pooling of water
Resolution:
-
Remediated the root cause of rust by fixing the multiple leaks
-
Removed the rust from components/equipment in the facility
-
Primed and painted the cleaned components with the approved materials
-
Sourced experts to determine best course of action with rusted pipes
-
Replaced all key piping, CLA valves, isolation valves, and the bladder tank
Violation: Black mold present on substantial portions of the ceiling including above and next to the finished water storage access hatch
Resolution:
-
Consulted with a mold remediation firm which determined that mold spores were in the wood and insulation
-
Sourced a credentialed industrial hygienist to prescribe a step-by-step remediation plan
-
Followed the protocol to remove all contaminated materials
Violation: Failure to have a monitoring plan
Resolution:
-
Discussed all of the monitoring components with the existing ORC and Administrator to gain the institutional knowledge of their operations
-
Analyzed the incorrect or missing parts of the plan and re-wrote the plan in entirety with the guidance of the CDPHE Manager
Violation: Failure to monitor for lead and copper
Resolution:
-
Established primary and alternative sampling sites
-
Worked with the ORC to submit samples for testing
Violation: Failure to have a Backflow Prevention and Cross-Connection Control Program
Resolution:
-
Discussed the status of all the water district buildings with the existing ORC, Administrator, the local Fire Chief, and a pertinent Condo Property Manager
-
Conducted physical surveys of suspected cross connections
-
Hired an outside specialist for backflow prevention device inspection and testing
-
Installed new backflow prevention devices per the guidance of the outside backflow prevention specialist
-
Provided all testing certifications to the CDPHE
Within 9 months Quality Water Management and the other constituents in the water district were able to get operations back into compliance.
Quality Water Management’s expertise, along with their ability to source and manage valuable professionals, provided the assistance needed to get the water district to where they needed to be.
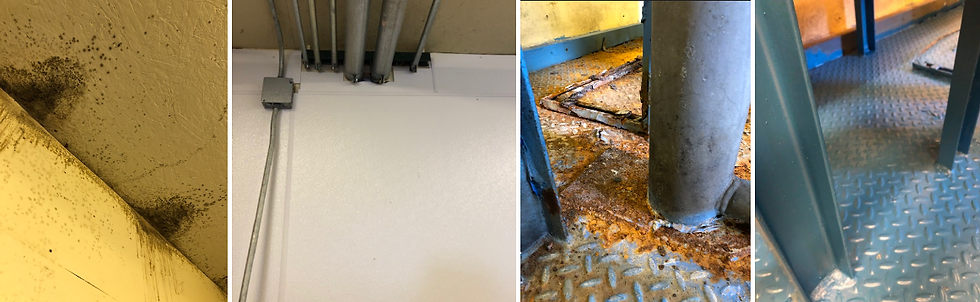
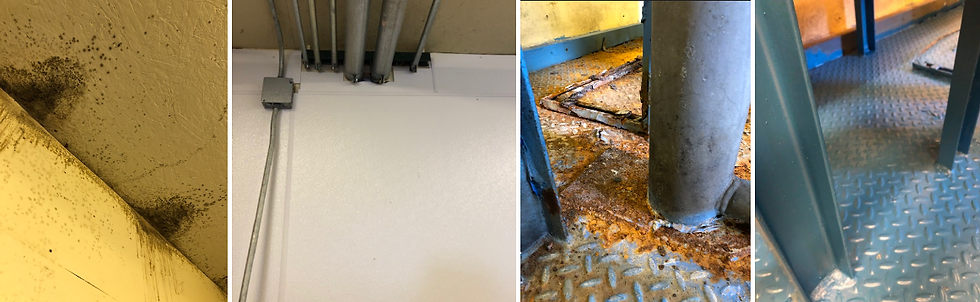